Innovation and Efficiency in Electric Defrost Evaporator Manufacturing
In the realm of refrigeration technology, the quest for improved efficiency, sustainability, and performance is ever-present. One critical component that has seen significant advancements is the electric defrost evaporator. This article delves into the innovations driving the manufacturing sector of these essential cooling system components.
Manufacturers of electric defrost evaporators are at the forefront of integrating cutting-edge technologies to enhance the freeze-thaw cycle's effectiveness. These devices prevent the accumulation of ice on the evaporator coils, which can impede airflow and reduce the overall cooling capacity. By using electrical heating elements to periodically melt away frost buildup, these systems maintain optimal operational performance.
One of the key trends in the manufacturing of electric defrost evaporators is the focus on energy efficiency. With global concerns over energy consumption and environmental impact, manufacturers are designing smarter defrost cycles. They incorporate sensor technology that detects the precise moment when frost formation reaches a level that affects performance, initiating the defrost process only when necessary. This demand-driven approach significantly reduces wasted energy compared to traditional timed defrost cycles.
Material innovation also plays a crucial role in enhancing the lifespan and efficiency of electric defrost evaporators. Manufacturers are exploring more corrosion-resistant materials and advanced coatings that can withstand the harsh environment of freezer units. Moreover, the use of lightweight materials helps reduce the overall load on refrigeration systems, further improving their energy efficiency Moreover, the use of lightweight materials helps reduce the overall load on refrigeration systems, further improving their energy efficiency
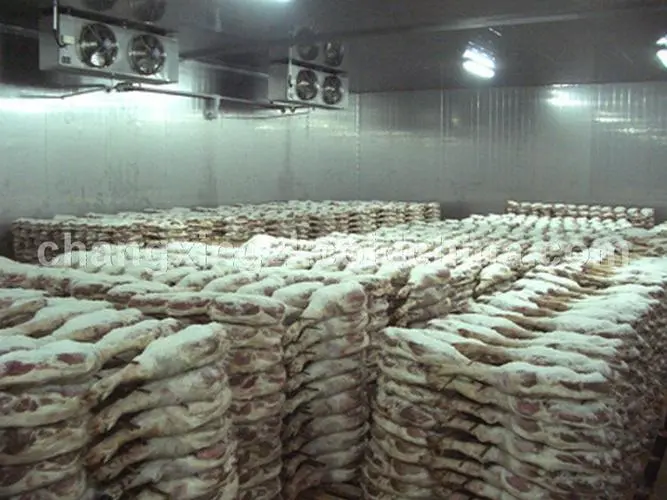
Moreover, the use of lightweight materials helps reduce the overall load on refrigeration systems, further improving their energy efficiency Moreover, the use of lightweight materials helps reduce the overall load on refrigeration systems, further improving their energy efficiency
electric defrost evaporator manufacturer.
Digital integration is yet another area where manufacturers are making strides. Connecting electric defrost evaporators to the internet of things (IoT) allows for remote monitoring and control. This capability provides data-driven insights into operational performance, enabling predictive maintenance and reducing downtime. It also facilitates seamless integration with smart building management systems, streamlining energy use across facilities.
The environmental footprint of manufacturing these components is increasingly under scrutiny as well. Leading manufacturers are adopting green practices such as using recycled materials and minimizing waste during production. They also design for recyclability, ensuring that products at the end of their life cycle can be disassembled and recycled effectively.
As we look to the future, the evolution of electric defrost evaporator manufacturing shows no signs of slowing down. With continued research and development, these devices will become even more efficient, reliable, and environmentally friendly. The industry's commitment to innovation ensures that refrigeration systems worldwide will operate at peak performance while minimizing energy use and environmental impact. As technology progresses, it paves the way for a new era of sustainable cooling solutions that benefit both businesses and the planet.