Industrial chiller compressors are indispensable components in the landscape of modern industrial operations. As the heart of a chiller system, they are pivotal in ensuring the efficient removal of heat from various processes, thereby stabilizing system operations and protecting equipment integrity. This article explores the nuances of industrial chiller compressors, providing an in-depth look into their functionality, types, and selection criteria, framed within the industry's best practices.
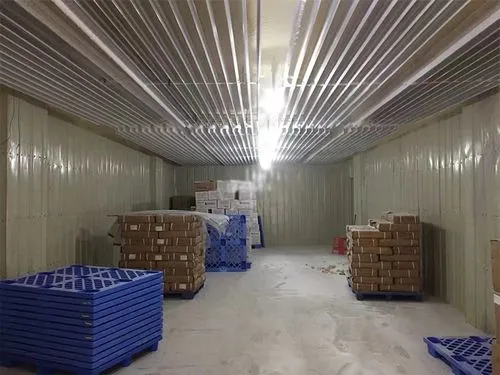
Industrial chiller compressors are primarily responsible for compressing refrigerant gas, a critical step in the refrigeration cycle. By doing so, they increase the refrigerant's pressure and temperature before it moves through a condenser, where the gas releases its heat and condenses into a liquid. This liquid then moves through an expansion valve and into an evaporator, where it absorbs heat and returns to a gas, ready to repeat the cycle.
When selecting an industrial chiller compressor, understanding the specific cooling requirements of an application is paramount. The choice between screw, scroll, rotary, reciprocating, and centrifugal compressors should be based on factors like load demands, energy efficiency, operational cost, and environmental considerations. For instance, screw compressors are renowned for their robust design and are highly effective in large-scale industrial applications requiring constant load and cooling output. They offer a balance between energy efficiency and reliability, which is critical in industries like pharmaceuticals and food processing.
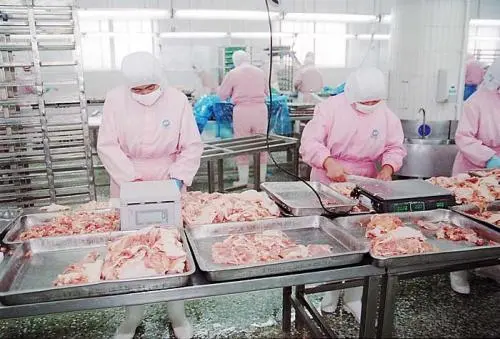
Scroll compressors, on the other hand, are designed for smaller-capacity applications. Their quiet and efficient operation makes them suitable for medium-sized industries where maintaining a stable internal environment is crucial. Their fewer moving parts contribute to a longer operational life and reduced maintenance, making them an attractive option for companies prioritizing sustainability and long-term cost savings.
For applications demanding a smaller footprint yet high efficiency, rotary compressors are an optimal choice. These are commonly used in applications with variable capacities and are known for their durability and efficiency. They are ideal for industrial sectors such as manufacturing and electronics, where precision and space-efficient solutions are needed.
china industrial chiller compressor
In high-capacity scenarios, centrifugal compressors are unparalleled. Their ability to handle large volumes of refrigerant with exceptional efficiency makes them a cornerstone in industries like automotive and heavy machinery. Although they have a higher initial cost, their operational excellence and longevity often justify the investment, providing businesses with reliable service over extensive periods.
In terms of energy efficiency and environmental impact, modern advancements in compressor technology cannot be overlooked. Variable speed drive (VSD) technology, for instance, enables compressors to adjust their speed based on real-time cooling requirements, dramatically reducing energy consumption and operational costs. This technological advancement also aligns with global sustainability trends, offering businesses an avenue to reduce their carbon footprint while potentially benefiting from government incentives aimed at promoting eco-friendly industrial practices.
Implementing the right industrial chiller compressor is not merely a matter of choosing the most advanced model. It necessitates a thorough assessment of an organization's operational demands, existing infrastructure, and future growth plans. Engaging with industry experts and consultants can provide valuable insights into optimizing chiller operations, driving both economic and operational benefits.
Maintenance is another critical factor in maximizing the life and efficacy of a chiller compressor. Regular inspections, system diagnostics, and timely overhauls ensure the compressor operates at peak efficiency and avoid costly downtimes. Leveraging predictive maintenance solutions powered by IoT technology can further enhance this process by providing real-time data and predictive analytics, helping in anticipating potential failures before they occur.
Choosing and maintaining the right industrial chiller compressor is crucial for ensuring operational excellence and sustainability in today's competitive industrial landscape. Through informed decision-making and leveraging cutting-edge technologies, industries can optimize their cooling processes, contributing not only to immediate financial savings but also to the broader goal of sustainable growth and development.